Introduction
Piezo benders, including unimorphs, bimorphs, and multi-morphs, are fascinating devices that utilize the piezoelectric effect to generate precise motion through mechanical displacement. These actuators consist of layers of piezoelectric material bonded with other materials, forming a composite structure capable of bending or flexing in response to electrical signals. With their unique properties, piezo benders find applications in precision positioning, ultrasonic devices, loudspeakers, haptic engines, and energy harvesting. In this article, we will explore the process of designing a unimorph piezo bender, considering key factors, materials, and techniques to ensure optimal functionality and performance.
Understanding piezo unimorphs
Piezo unimorphs consist of a single layer of piezoelectric material attached to a substrate layer. The piezoelectric material exhibits the property of generating an electric charge when subjected to mechanical stress or vice versa, resulting in mechanical deformation when an electric field is applied. In a piezo unimorph, this deformation primarily occurs as bending or flexing due to the differential expansion and contraction between the piezoelectric layer and the substrate layer. This configuration enables controlled and precise movement or displacement, making piezo unimorphs valuable in various applications such as actuators, sensors, and microelectromechanical systems (MEMS).
Material Selection
Piezoelectric materials
Piezoelectric materials like PZT (lead zirconate titanate) materials including PZT-5A and PZT-5H are popular choices for piezo actuator design due to their exceptional properties. PZT 5A boasts a high electromechanical coupling coefficient, enabling efficient energy conversion between electrical and mechanical domains. It excels in applications requiring significant displacements, such as ultrasonic actuators and precision positioning systems. PZT 5H, on the other hand, offers a higher piezoelectric strain constant, making it suitable for applications demanding large force output and high stiffness, such as piezo motors and robotic systems. PVDF (polyvinylidene fluoride), a polymer-based material, possesses unique properties suitable for specific piezo actuator designs. It offers flexibility, low density, high dielectric strength, and excellent resistance to moisture, chemicals, and UV radiation. PVDF is easily processed into thin films and finds applications in wearable devices, medical sensors, and acoustic transducers.
Substrate materials
The choice of substrate material significantly impacts the overall performance and functionality of the piezo bender. Common substrate materials include aluminum, stainless steel, glass, ceramic, and polymer. Aluminum provides lightweight construction, high stiffness, and excellent thermal conductivity, making it suitable for applications requiring rigidity and thermal stability. Stainless steel offers mechanical strength, corrosion resistance, and dimensional stability, ensuring durability in challenging environmental conditions. Glass substrates possess high electrical insulation properties and smooth surface finish, making them ideal for applications involving optics. Ceramic substrates, with their excellent electrical insulation and thermal stability, find use in high-temperature applications and those requiring precise dimensional control. Polymer substrates offer lightweight, flexibility, and good electrical insulation properties, catering to applications requiring conformability or flexibility.
Design considerations
Dimensions and geometry
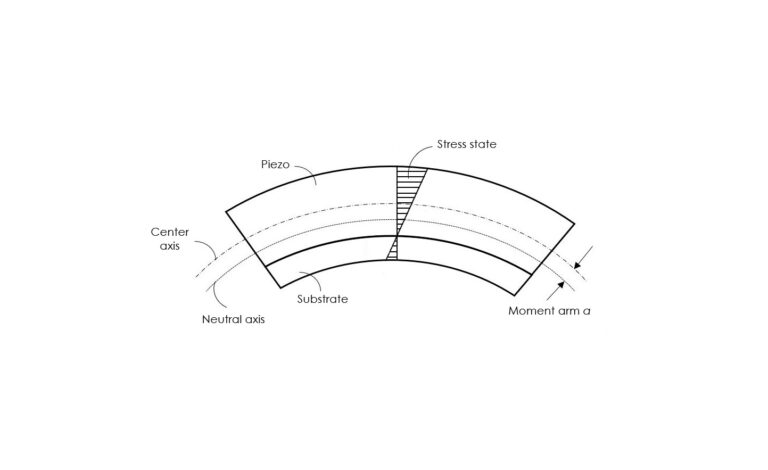
The dimensions and geometry of piezo unimorphs significantly influence their performance. Engineers must strike a balance between displacement/deflection and blocking force. Factors such as material stiffness, substrate thickness, and shape influence the unimorph’s performance. Thicker or more rigid substrates increase bending stiffness, while longer moment arms enhance displacement. Numerical simulations and design of experiments (DOEs) can be utilized to optimize the dimensions and geometry of the unimorph. Advanced bending actuators, such as those offered by Flora, incorporate complex multi-layered substrates and protective layers, ensuring both performance and reliability across various applications.
Resonance frequency
Understanding the impact of materials and dimensions on the resonance frequency of the unimorph is crucial. Excessive displacement at resonance can lead to cracks and damage. Therefore, it is essential to consider resonance frequency during the design process to ensure the unimorph operates within safe limits for the intended application.
Mechanical and electrical integration
Proper mechanical and electrical integration is vital for the successful functioning of the piezo unimorph. It is crucial to consider mechanical constraints and electrical integration early in the design process to ensure compatibility and seamless operation within the desired system.
Conclusion
Designing a unimorph piezo bender requires careful consideration of materials, dimensions, and fabrication techniques to achieve desired performance characteristics. By comprehending the fundamental principles and following the guidelines presented in this article, engineers and researchers can create efficient and reliable piezo unimorphs for a wide range of applications. It is advisable to consult relevant literature, research papers, and experienced professionals for comprehensive and detailed guidance tailored to specific project requirements when undertaking the design and fabrication of piezo unimorphs.